Choosing a thermal transfer overprinter: 7 key considerations
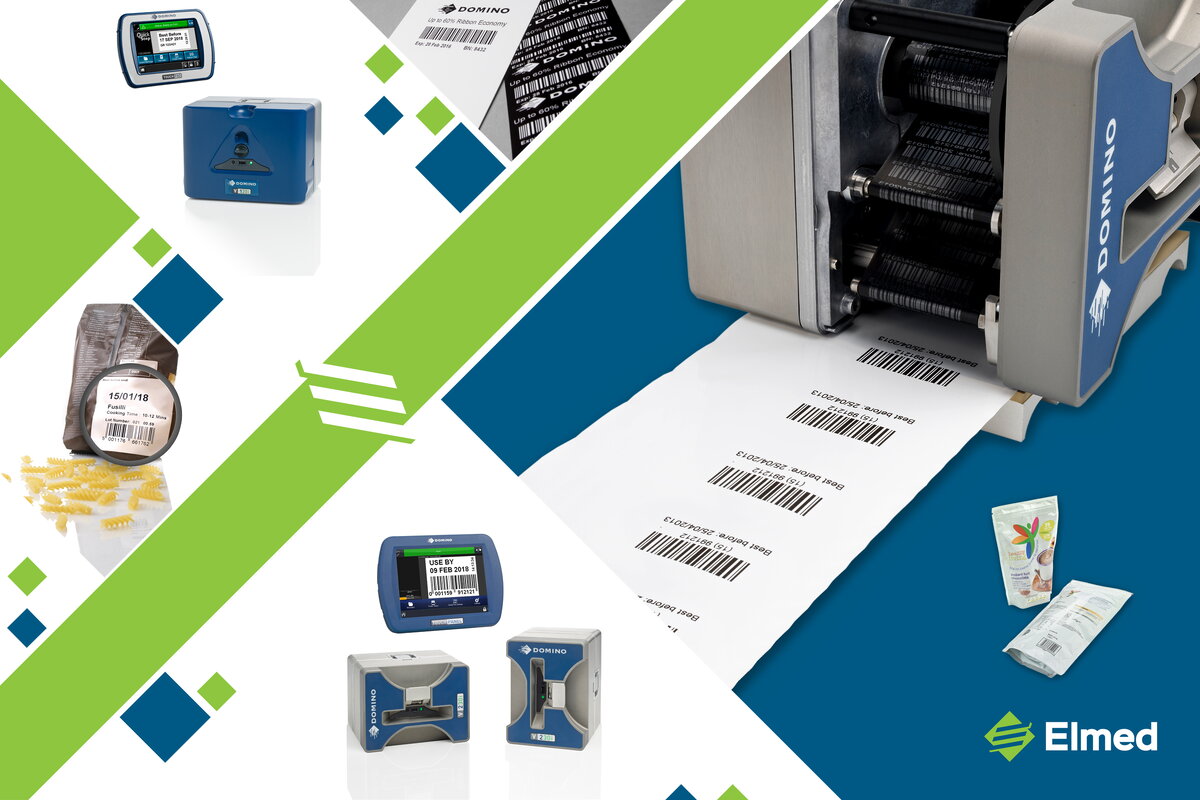
It’s about more than just the printer model you choose. Getting the best from thermal transfer overprinting technology requires finding a supplier who can optimise the technology for your production line and minimise downtime with support that’s there when you need it. Here are seven key considerations when choosing a TTO supplier.
Why use thermal transfer overprinting (TTO)?
The major benefit of TTO is that it’s exceptionally good at providing high quality printing on to flexible packaging materials and labels. It’s a speedy way to print everything from simple best before dates and batch codes to logos, product descriptions, nutritional panels, fully compliant barcodes and more. TTO is especially cost-effective in sectors with multiple SKUs and high output such as food, pharmaceuticals, beverage and tobacco.
The best option for your business. That’s what you’re looking for.
When you are choosing TTO technology, you understandably want to make the best choice for your business. Print quality and speed is all important. But you should also look past the fundamentals and consider the less obvious things too.
For instance, you need to make sure your printer is perfectly optimised for your production environment and delivers all the flexibility you require. You should also look for a supplier who works with you to minimise downtime and provides support that you can count on when time is of the essence. The eco-credentials of your TTO technology may be important too - whether that’s from a cost-savings point of view or in terms of contributing to your corporate social responsibility efforts.
Whether you are looking for a new TTO supplier or are exploring TTO technology for the first time, here are seven key considerations to make sure you get the best option for both your production environment and your bottom line.
1. What bracketry is required?
You’re not going to get far with TTO unless you have the right bracketry to support your technology. Ask your supplier if they supply this and whether it’s included in the cost of your purchase. The right set up will ensure your printer delivers all the flexibility you need and is optimised for your production environment.
Domino’s V-Series V120i and V230i models are small, compact and capable of fitting neatly into almost all existing thermal transfer brackets. That’s ideal for production environments where space is already at a premium. It will make for speedier, cheaper installations too, especially when replacing existing ageing, tired equipment.
2. What’s your stance on compressed air?
Most TTO systems require compressed air. That could mean costly alterations to the infrastructure of your production facilities. It’s also important to consider the environmental impact of your technology - and when it comes to Mother Nature, compressed air isn’t ideal.
Domino’s V120i and V230i are all-electric with no need for the use of compressed air. That allows you to print at high speed in a way that’s easier on both the environment and your operational costs. One more thing. Domino’s TTO technology uses a unique ‘dancing arm’ drive to maintain ribbon tension. It virtually eliminates downtime and means you can use up to 60% less ribbon.
3. Will your TTO technology integrate?
Your production line should be a cohesive system of different parts working together in unison - rather than different technologies working independently of one another. Will your new technology be able to communicate with your existing printer control system? Can it be controlled via your existing HMI? Integrated systems create a streamlined, efficient production line that’s predictable, reliable and easy to control. Switching between jobs and controlling production has to be easy. You are too busy for fiddling around and balancing mis-matched internal systems.
4. Installation time
Downtime costs money. You need to make sure your new printer is installed not just so that it is optimised for your production line, but in a way that minimises disruption to your operations and keeps downtime to the absolute minimum. That may mean looking for a supplier who is flexible enough to install your TTO technology at a time that suits your production schedule - even if that’s in the middle of the night.
5. Data management speed
How quickly can your chosen model handle data transfer? Can it accommodate the data volumes and speeds you require on your production site? And does it have the ability to meet your future production requirements? Aim for technology that will stand the test of time and meet your production demands as your business grows.
6. What about servicing and support?
If your printer goes down, it’s a business emergency. So it’s important to scrutinise your supplier’s service and support provision. Do they offer telephone support? How quickly can engineers be at your site? How many field engineers do they really have? And do they stock replacement parts?
7. Does your supplier meet health and safety requirements?
Health and safety: three words that tend to induce sighs. But it’s important. Make sure your technology is certified to the necessary regulatory standards and installed by properly trained experts. Also check that ribbons meet safety standards such as EuPIA GMP.
What next?
Take a look at our V-Series. It’s a highly advanced range of TTO technology that’s great for your bottom line. Designed for crisp, clear coding, the V-Series delivers the highest resolutions (300dpi) at the fastest speeds in the industry. As the leading global supplier of coding and traceability technology for the food, pharmaceutical, medical and industrial sectors, you can trust our commitment to your production goals and performance. Come and find out more.