Future on board, maintenance on site
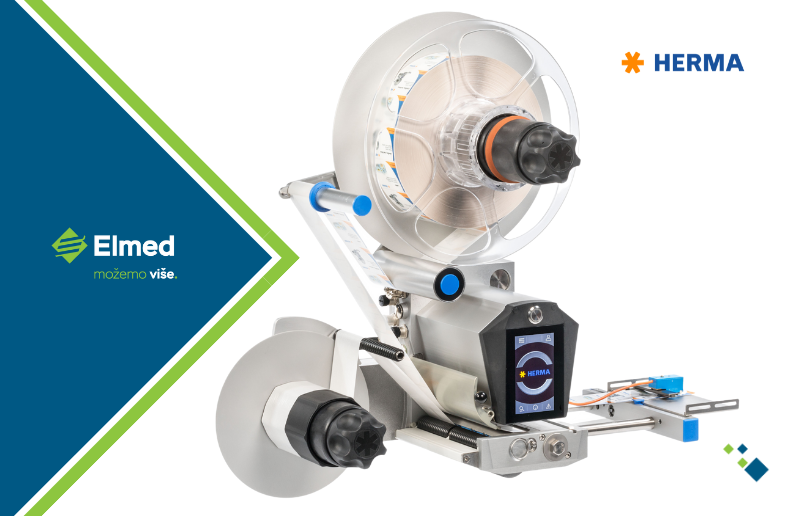
New innovative features for the HERMA 500 label applicator
- An industry-wide first introduces code-enabled upgrades to make the HERMA 500 applicator even more flexible and future-proof.
- The ability to exchange key components on-site likewise enhances ease of maintenance and machine availability in everyday operations.
Enhanced performance at the push of a button – what the car pioneer Tesla has successfully demonstrated is now available for the HERMA 500 applicator as well. With the aid of a code, which is simply and uniquely purchased online and delivered automatically by e-mail, upgrades for additional functions or higher speeds can now be installed without booking a service appointment with the manufacturer. What’s more, critical components of the applicator can now be exchanged easily on the operator’s premises, thus avoiding a time-consuming visit to a service centre.
“For us, the key question was how could we substantially further improve an applicator’s availability,” explains Tobias Erhardt, who heads up the service department for HERMA Labeling Machines. “The answer was found in the realization that long-term efficiency and effectiveness depend to a large extent on the ease of maintenance and the ability of the user to respond quickly to new challenges without significantly interrupting production.” In order to achieve these goals, we equip the HERMA 500 from the outset with a series of options that users may wish to activate and use later.
A good example is a connectivity. “Instead of configuring an applicator for the individual customer’s specific requirements, all the principal connectors are already on board. Only those for Industrial Ethernet and Power Out are now optional.” One function that is often requested subsequently is the master encoder. It is responsible for maintaining absolute synchronization between the operating speed of the applicator and that of the conveyor belt. As a result, the encoder achieves greater labelling precision and reliability.
“ In the past, the applicator had to be rebuilt quite time-consumingly for this purpose if the connection for it was not yet available. Now it’s simply a matter of the customer enabling the function with a code.” Users can also apply the same method if a need arises for higher speeds, OPC UA or Modbus TCP interfaces, or machine control via CAN bus.
The whole package of measures
With immediate effect, smart design details of the HERMA 500 help users eliminate the causes of unscheduled downtimes even faster. If necessary, both the main and the plug-in circuit boards can now be exchanged on-site by a local service partner. The task involves little more than slackening off a few screws. There is no longer any need for wiring work, which previously called for a visit to a service centre. HERMA has also further reduced the number of wearing parts and is committed to using standardized components that are available worldwide. In addition, no special tools are needed to exchange the transport roller. What’s more, most of the connectors are now being embedded in the housing, where they are well protected against accidental impacts. And the outgoing cabling is integrated into a single loom, which further simplifies integration. “This package of measures enables us once again to redefine the boundaries of maximum applicator availability in practice, no matter what the circumstances,” insists Head of Service Tobias Erhardt. “At the same time, the HERMA 500 is further demonstrating its credentials as an especially future-proof investment.”
In case you are interested in buying the new enabling codes, feel free to contact us at office@elmedint.com
*Text is taken from the website https://www.herma.com/machines/about-herma/news/detail/future-on-board-maintenance-on-site/