Inspecting variable data
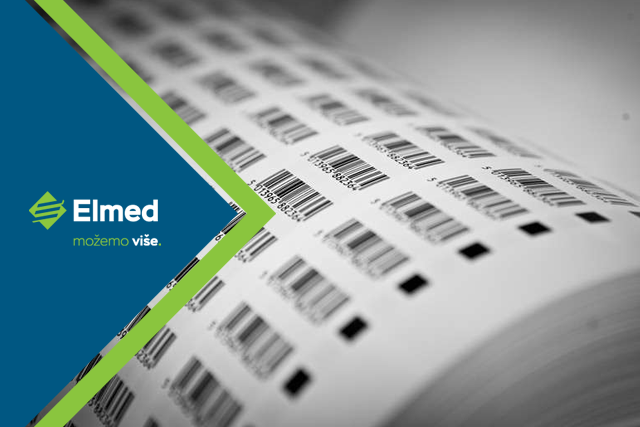
Producing a high quality label effectively and efficiently has always been and always will be the ultimate aim of any label converter. Getting it right first time and eliminating waste is the main principle that should determine their working practices.
Over recent years JIT workflows have been at the forefront of the way in which production and deliveries are planned. However, the current pandemic has thrust even more pressure on getting labels to the product manufacturer, especially in the food and pharmaceutical sectors which have seen vast increases in volumes in order to support the supply chain of products to the supermarket sector in particular.
Figures from a recent Finat survey of members show that there was an increase of almost 7 percent in the demand for labels in the first quarter of this year compared with 2019. The current and future quarter results are forecast to be severely impacted by the Covid-19 outbreak and subsequent lockdowns in countries around Europe since March.
This short term demand for critical supplies to the food, pharmaceutical and medical markets has increased considerably and been caused by the start of a stockpiling philosophy in anticipation of prolonged lockdown periods and consumer hoarding.
In view of this uncharacteristic behavior, it should be no surprise that lead times for self-adhesive materials, especially for non-critical goods, have increased substantially. Apart from the availability of raw materials (not only self-adhesive materials but also critical chemicals for the manufacture of consumables such as inks, adhesives and silicones), label converters are facing the impact of lockdowns through the reduced availability of staff on the shop floor. This has meant adjustments to working practices necessary to comply with tightened operational safety and health measures (OSHA), and cashflow issues related to unilateral extension of payment terms by customers. (compiled from the Finat Q1 report on the state of the European label industry).
All of this means that it is vital that converters, whilst working to ever shorter delivery times, are confident that their output is right first time and waste is kept to an absolute minimum.
Web inspection
In the past we have discussed web inspection from the point of view of the finished, printed label. In this article we discuss the verification of the added variable data which can be so important to the end user, especially in the food, pharmaceutical, security and anticounterfeit sectors where incorrect or missing information data can be vital to the end user or consumer. Whilst many label converters use a narrow web, single width roll to print labels, to maintain production levels in these times of high demand and to meet the requirement to print several SKUs simultaneously, converters are using multi-lane production methods. This makes the task of inspecting several tracks of labels with different images very demanding, especially when variable data is involved.
For variable data labels it is important to inspect every label and code and verify that it is correct against the original data file. It is also important to ensure that the quality and security features are accurate. Lake Image Systems recently introduced its Discovery Label Integrity Manager (LIM) which consists of an automated inspection system for verifying variable data which is printed on high-speed, multi-lane label presses. The LIM automates the finishing of the individual rolls whilst building in integrity, control, reporting and management to high levels of reliability.
Automating the inspection of the variable data components of a label printed using multi-lane technology when compared to single web production brings several significant benefits to the converter. This has been proved in practice at least two sites, one a major European security printer and the other a global security printer. The challenge was to ensure that the integrity of every reel was intact and the whole process to be automated. Benefits include increased label production rates – an increase of around 20 percent at the two sites.
Slitting the parent rolls into single webs has proved to be more cost effective and produce less waste. Automating the inspection process has significantly reduced the time and labor costs of the QA function. Using automated inspection eliminates the human error element greatly, reducing the chance of reprinting and reruns. Up to 15 percent less scrap has been experienced at the two client sites.
One more benefit is the automatic production of an error log which can prove invaluable when removing defective labels with incorrect or missing data. This is achieved by producing a mapping file with each reel, which in turn provides a closure report indicating any errors which have occurred during the production of the reel including breakages, unreadable or missing labels.
The result is a quality audit of each individual reel and the opportunity to mark defective labels as void using an integrated inkjet printer.
Overall this automation is a good fit with Industry 4.0, which requires automation of inspection (and other processes) and can integrate seamlessly into an automated production workflow for the Industry 4.0 protocol. It also means that the label converter is able to monitor the print quality of their output in real time. This allows converters to calibrate their printing systems, be they conventional or digital when (or if) an error is detected. This enables the converter to operate a zero defects protocol, for pharmaceutical or security labels for example, and thereby meet these end users’ most stringent quality standards.
Modern inspection systems can also be set up to communicate with MIS systems connected to a pharmaceutical of security track and trace system.
Automated inspection systems also offer environmental benefits which means that costly reprinting and is avoided and significant less waste of substrate, ink is produced and a saving in production time is achieved.